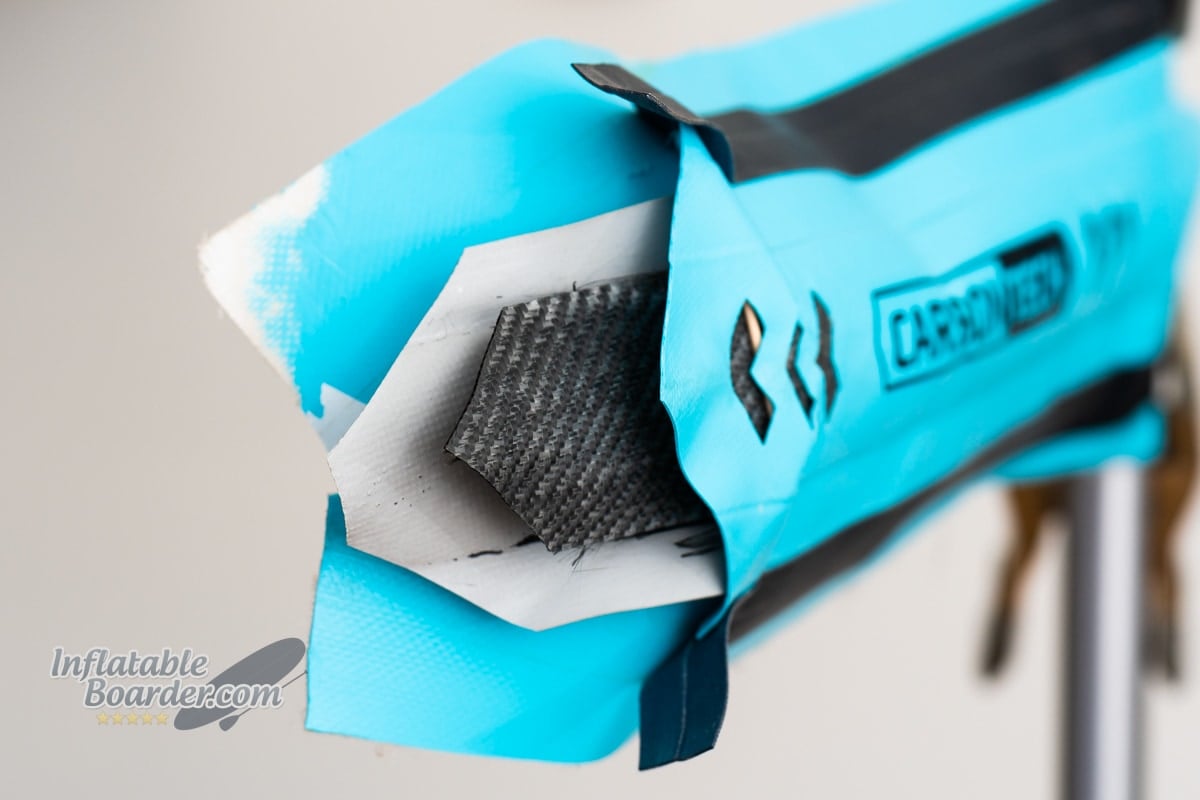
How a paddleboard is built can impact its longevity and performance as much as its size and shape. Brands have a huge amount of choice when it comes to the actual materials and construction types, however all iSUPs follow the same basic structure. In this article, we’re going to go through the parts of an iSUP, some of the variations in materials and construction, and de-mystify the marketing jargon surrounding iSUP construction.
Building an iSUP
In the simplest forms there are only three parts of any iSUP: the drop stitch core, the air-tight shell, and then any additional features on the exterior of the board. You technically have a functional iSUP after just the first two items, but not one that’s very user-friendly!
Drop Stitch Core
Every inflatable paddleboard uses a type of material commonly referred to as “drop stitch” at the core of the board. Drop stitch fabric is made of three parts: a top and bottom fabric layer and “space yarns” which connect the fabric layers together. Sometimes the space yarns are referred to as “drop stitching,” so it can get a little confusing at times when reading through descriptions and specifications.

There are different types of drop stitch material that can be used for iSUPs, but they all provide the same basic function. The space yarns are woven into the fabric on one side, then threaded across to the fabric on the other side. This process repeats thousands of times for each paddleboard. The space yarns are what set the thickness of the paddleboard and provide the structure to keep the paddleboard flat when inflated, rather than rounding out like a balloon.

PVC Shell
iSUPs use at least one layer of a PVC material* in order to create the airtight, rigid shell that becomes the deck, hull, and rails of your paddleboard. This material can be made of different thicknesses, contain different reinforcements, and can be layered for additional rigidity and durability. The PVC shell is attached to the drop stitch fabric in one of several different ways.
Several years ago the quality of an inflatable paddleboard was almost universally tied to the number of PVC material layers it had. Thanks to advancing technology this is no longer the case.

The top and bottom of the shell are joined together with a strip of PVC material that wraps around the rails, or sides, of the board. This rail band is what holds the air tight chamber together. There are usually multiple layers on the rail of the board for increased durability and stiffness.

There can also be additional structural components within or added to the outside of the PVC shell. These can include stringers – thin pieces of PVC or other material that run the length of the board – and composite rail reinforcements. These structural components are added to increase rigidity and help maintain the board’s shape.

*There are a few paddleboard models that use a TPU material instead of PVC, however they are very few and far between.
Exterior Features
Once the drop stitch core and PVC shell are joined and sealed with the PVC rail band, the board is air tight and technically usable. Though if you’ve ever tried standing on the bare PVC of an iSUP, you know just how slippery of a situation that can be! External features like deck pads, fin boxes, d-rings, and more are glued to the paddleboard at the end of the manufacturing process.
Building an iSUP: Putting It All Together
Deciding how to actually put the core components of an iSUP together is just as important as selecting the right materials. We refer to this process and result as a paddleboard’s construction.
The drop stitch core fabric is woven or knitted together, then the two layers are stitched together by the space yarns. The lowest-cost and lowest-quality single-layer iSUPs are made by coating the fabric layer with liquid PVC before being cut to shape and adding the rail bands.
Traditional double-layer iSUPs start with the same process, but adds a layer of PVC tarpaulin (PVC plastic reinforced with a fiber mesh) through a hand-gluing process.

Fusion PVC is a newer technology that uses heat and machine lamination to apply this second (and any subsequent) layer without the use of an adhesive. Fusion constructions reduce weight, reduce the chance for manufacturing errors, and can create a more rigid and durable iSUP.
Both traditional and fusion laminations occur at the raw materials phase before the material is cut to shape.

Graphics can be screen printed or laminated onto the PVC shell either before or after the material is cut to the appropriate size and shape. If there are any external stringers added to the board they are normally applied at this phase.
Once the core/shell material is cut to the right shape, the inner rail band is added to complete the airtight chamber. This inner rail band (often referred to as the seam) can be glued or welded. Adhesives create a chemical bond between the different layers of materials to hold them together. Heat-fusing, or Welding, lightly melts the PVC on the two surfaces before pressing them together and cooling to create a physical bond that essentially turns the two parts into one continuous piece of PVC. Both methods have positives and negatives, however welding and heat-fusion are typically considered to be superior to adhesives. This does not mean that adhesives are “bad.” It’s more like the difference between a wood-stud or metal-stud structure. Both are equally valid methods of construction with different features and purposes.
Lastly, all remaining external features of the board are glued into place. This includes handles, d-rings, fin boxes, and deck pads.
De-Mystifying Marketing Slang
In a perfect world we could all agree on using the same terminology to help reduce confusion. It can be hard enough ordering a drink in an area where “coke” can mean any type of soft drink, and likewise it can be hard to truly compare paddleboards when brands use different terminology or Trade Names to refer to the same or similar thing.
We’re going to start with my biggest pet peeve in the industry: “Military Grade.” For inflatable SUPs, this is often used to describe the PVC shell material. And sometimes it gets thrown around even more generally than that.
I asked several of my veteran friends what they felt about the term “Military Grade” and was met with the same answer each time: A loud “Ha!” followed by a rant… The problem is “Military Grade” doesn’t actually have a meaning. It’s used to imply durability and strength, but as pointed out to me time and again, the military buys a lot of stuff, and they only buy it with the cheapest price that meets their bare minimum need, and that doesn’t always pan out well (or get used at all). There are no standards used by the military for stand up paddleboards, and thus “Military Grade” is completely meaningless.
Tirade aside, If you see the term “Military Grade,” just ignore it. You’ll never see that word used in our reviews as it has no meaning and no specification. It’s simply a buzzword designed to make you think something is strong without actually providing any proof or detail for that claim.
What about running a paddleboard over with a truck, or other machinery? Well, that is a pretty cool thing to show, but it doesn’t really tell you anything about the board. These demonstrations can also be misleading (there’s no way to put the entire weight of one of these vehicles on the board at once). At best they simply show you that under controlled conditions, that are in no-way related to paddling, the board doesn’t “pop.”
Fusion Materials/ Fusion PVC
Fusion PVC is a term that is used to describe a laminating process that physically bonds two layers together without adhesive.
The core concept of Fusion PVC is that by using heat and a machine lamination process to melt and bond the PVC materials together you eliminate weight from adhesive between PVC layers, create a more cohesive structural layer, and eliminate defects that can come from the hand-glued lamination process. That doesn’t necessarily mean traditional laminations are bad, it’s just a different process.
MSL
MSL is an acronym created by Red Paddle Co. that is short for Monocoque Structural Laminate. Red uses this term to describe the process in which they adhere their PVC shell to the drop stitch core. MSL uses a particular adhesive between the raw fabric layer and the PVC material and machine lamination to combine them rather than coating the fabric layer in liquid PVC and partially melting it during a fusion lamination process. The process and adhesive together are Red’s proprietary MSL construction method. Other brands that use this trade name are doing so without Red’s permission, and are likely not using the same MSL process to begin with. Many times MSL is used by other brands, incorrectly, to refer to Fusion PVC layers.
PVC Layers – Single, Double, Triple Layer iSUPs
Several years ago, iSUP rigidity and durability was determined mostly by how many layers of PVC material were used to create the board’s shell. Thankfully for us as paddlers those days have long passed. However, there is still some kernel of truth here, and of course lots of confusion on the matter.
The best thing to remember is: Not all materials are the same! Just because iSUP A is single layer and iSUP B is double layer, doesn’t automatically mean that iSUP B is stiffer or more durable. Technically Red Paddle Co.’s MSL construction is a single-layer PVC board! There are lots of new and different materials used in the industry with different properties. However, most iSUP brands do not provide explicit specifications of the materials they use. They’ll only tell you how many “layers” of material are used (and sometimes they won’t even tell you that). But even the number of layers cannot always be taken at face value. It depends on what each brand considers to be a “layer” and where they are counting from (the hull or the rail).
Okay, so what do you do when shopping for an iSUP? How are you supposed to really know how many layers of PVC there are? How are you supposed to know if the number of layers is even important for a particular board?
The truth of the matter is, it’s nearly impossible to know for sure. This is why we thoroughly test each board we review. By checking real-world weights and using standardized rigidity testing (plus real-world on-the-water testing) across all brands and models, we are able to comparatively decipher many of these construction mysteries. We can both quantitatively and qualitatively identify the most rigid boards regardless of how many layers they do or do not have (or if that even matters). With our data, we can confidently say that none of the brands we have tested are using three separate layers of PVC material for the PVC shell of their iSUPs. However, we still see excellent results in our rigidity and performance testing.
On the flip side, “Spec Reviews” that many publications write (particularly major publications that have nothing to do with SUP or paddlesports generally) that simply regurgitate the descriptions and specifications from the brand themselves offer no actual help or insight to readers. We could spec review every iSUP on the market, but it’s not going to help anyone. We focus on honest, real-world, reviews of products we use.
Woven or Knitted and Linear or Crossed Drop Stitch
Here we have a few terms that do actually describe part of an iSUP, however they aren’t always used clearly. These terms are typically used to describe how the parts of the drop stitch core are made.
The top and bottom fabric layers can be made of Knitted fibers that create an interlocking ‘U’ pattern (just like knitting a sweater), or the fibers can be Woven with straight-line warp and weft yarns (like a woven blanket or rug). Because woven fibers run in straight lines along the length and width of the material, there is less “slack” in the fabric itself and thus less bend when under pressure. This makes woven fabrics lighter and stiffer than knitted fabrics, but they are slower and more costly to produce. If the fabric material isn’t specified it’s a safe bet that it is a standard knitted fabric layer.
Some brands also use the term “Woven” to describe the space yarns – the fibers that run between the fabric layers to give an iSUP a flat shape. Rather than referring to the space yarns as being “woven” we use, and are promoting the use of, “crossed” space yarns. Crossed space yarns run at an angle to the top and bottom fabric layers (alternating direction with each row of yarns), Standard space yarns make a V pattern without crossing over in alternating rows, and Linear space yarns run vertically between the layers. New materials and new designs make these differentiates even harder since we are unable to actually see inside the paddleboards to verify.

Stringers and Carbon Fiber/Composite Reinforcements
Stringers are pieces of material (usually PVC, but also composite materials) that run the length of a paddleboard – usually through the centerline of the board. In a rigid board, stringers are normally made of wood and are set vertically within the board between the deck and hull. In inflatable SUPs, stringers are glued or welded flat to the deck or hull (or both). Stringers serve two purposes in iSUPs. They can help maintain the rocker profile of the board (how much the board bends up at the nose or tail) and they can add rigidity at a much lower weight penalty than a full layer of PVC material. Some stringers are even built with composite materials, like carbon fiber fabric, to reduce flex even further.
Carbon fiber, and other composite materials, can also be used to reinforce the rails (sides) of an iSUP. The rail reinforcements work differently than the stringer reinforcements, and the fabric versions of these work differently than the plastic composite versions. The carbon fiber fabrics, though thicker than PVC, only marginally increase rigidity by increasing vertical strength. However they do prevent the rails from flexing to the sides much better than PVC alone. While it’s not particularly visible, any time you step on an iSUP, the rails bulge slightly to the side as the deck is compressed toward the hull. By resisting this sideways bulge, the fabric reinforcements increase the board’s rigidity and spread any flex out along a longer area.
It is important to remember that this is not the same type of carbon fiber material that is used to make SUP paddles, model airplanes, or expensive supercars. This carbon fiber fabric is typically thicker and is treated with a flexible stabilizing resin rather than a rigid epoxy or polyester resin (used to create rigid carbon fiber sheets and tubes). This allows the fabric material to bend and flex when rolling and storing your iSUP.
Carbon fiber and plastic reinforcements can also be used to reinforce an iSUP. These are often used as partial stringers that run through the middle ⅔ of the board on the deck and hull. The carbon fiber yarns and plastic matrix help spread out any flex from the standing area over a longer distance, creating a flatter and less-pronounced curve.
The Red Paddle Co. RSS (Rocker Stiffening System) battens work like a combination of these technologies. The fiberglass battens are extremely stiff vertically and help spread out the flex from the standing area into a smaller and smoother arc rather than a deeper, sharper bend. The wonderful thing about the RSS battens is they are removable – so we were able to test their impact on the same board. We found the RSS battens reduced the overall bend depth of the Red Elite 12’6” by ⅛ inch (3.2mm) in our bend test. While this may not seem like a large result, it represents a 10% improvement and doesn’t include the paddling benefit of having a smoother rocker line compared to a sharper bend at the standing area.

iSUP Construction: Final Thoughts
While the last 3000 or so words may not make it seem this way, we’ve only just touched on the surface of iSUP construction. There are so many more options and variables out there available for manufacturers, and more in development each year.
The key things to look for in any iSUP construction are brands that provide open and honest details about the materials and methods used in making their paddleboards, and the brand’s overall performance history. Like with all things, you do get what you pay for with iSUPs. The incredibly cheap paddleboards available on amazon have been known to literally fall apart or fail on their first use (I know, I used to run a shop that did repairs!). While it doesn’t take thousands of dollars to find a good inflatable paddleboard, spending the money on a quality board from a reputable brand is always going to produce a longer-lived and better performing iSUP than opting for the cheapest available.
While the specific materials and construction techniques aren’t always apparent in every board, even to us, our continued standardized testing and data-driven reviews can help shed some light on how well these paddleboards are made.
If you do have any questions about iSUP construction, always feel free to reach out to the brands directly, or drop us a line using the contact us form at the bottom of this page.